www.engenharia-brasil.com
06
'21
Written on Modified on
Reduzir o custo por peça
Para lidar com mercados flutuantes, os fabricantes devem rever todo o processo de torneamento de aço.
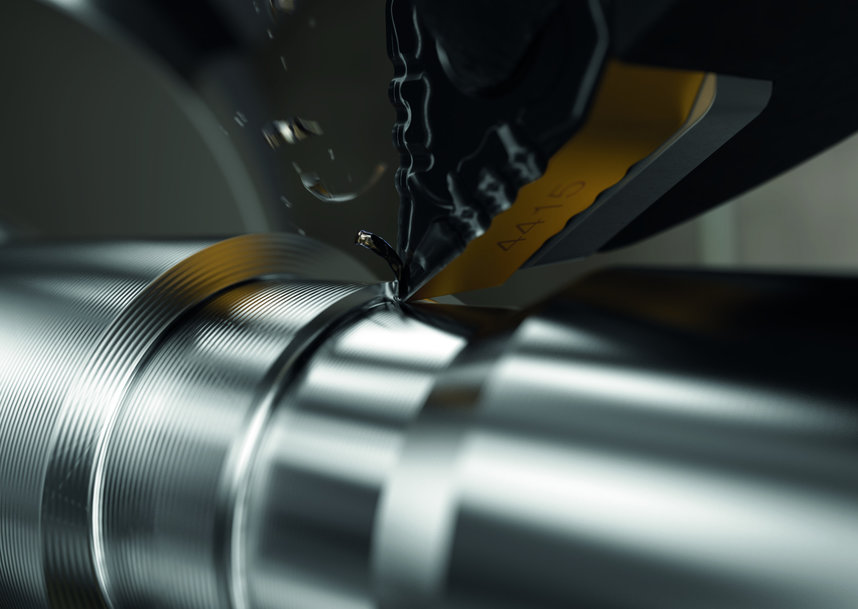
Um inquérito realizado pela associação nacional de fabricantes norte-americana (NAM) demonstrou que 53% dos fabricantes prevêem que a COVID-19 terá impacto nas suas operações, pelo que os fabricantes estão a sofrer uma pressão cada vez maior para serem competitivos — incluindo na produção em massa que envolve componentes em aço duro. Neste artigo, Rolf Olofsson, gestor de produto da Sandvik Coromant, líder mundial de ferramentas de corte de metais, examina de que forma uma abordagem alternativa às operações de torneamento de aço ajuda a optimizar os seus custos por peça e a rentabilidade geral.
A economia de produção determina a rentabilidade de uma empresa. No corte de metais, a economia de produção deve concentrar-se em assegurar que estes processos e ambientes são seguros e previsíveis. Deve haver dois grandes objectivos: em primeiro lugar, manter o máximo rendimento de produção e, em segundo lugar, o custo de produção mais baixo possível, sendo que cada objectivo se revela apropriado para uma situação específica do fabricante.
Estes objectivos colocam desafios às operações de torneamento de aço que podem deparar-se com limitações, desacelerações da produção ou restrições no número de componentes produzidos por ciclo. E, agora, há os desafios mais abrangentes colocados à indústria pela COVID-19. Em resposta à estatística dos 53% da NAM, a Pricewaterhouse Coopers referiu: "Essas previsões sombrias já se estão a tornar realidade, conforme demonstram a descida a pique dos preços do petróleo e da procura, as limitações da cadeia de abastecimento, a desaceleração do consumo e a instabilidade dos mercados de crédito."
Os fabricantes, particularmente na produção em massa, estão especialmente conscientes do custo por peça ao efectuarem a gestão das suas operações de torneamento de aço. O princípio básico do custo por peça é calculado pela soma dos custos fixos totais com os custos variáveis totais, dividida pela total de unidades produzidas. Os parâmetros do torneamento de aço dependem também substancialmente da procura do mercado, visando a redução dos custos de produção ou o aumento da capacidade produtiva.
As empresas que fabricam componentes automóveis, por exemplo, poderão enfrentar cenários de elevada ou reduzida procura no futuro. Cenários de reduzida procura exigem ferramentas capazes de produzir mais peças por aresta, garantindo, simultaneamente, a segurança dos processos com menor número de rejeições de componentes. Cenários de elevada procura necessitam de soluções de ferramentas que permitam maiores taxas de remoção de metal, tempos de ciclo reduzidos e aumentar a utilização da máquina com interrupções mínimas da produção.
Independentemente do cenário que enfrentam, os fabricantes devem procurar maximizar a sua capacidade de maquinagem, que, de acordo com as conclusões da Sandvik Coromant, pode reduzir os custos dos componentes em 15%. Mas, para o conseguirem, ao mesmo tempo que maximizam a segurança dos processos, a resposta pode estar numa abordagem alternativa às ferramentas.
Redução do tempo sem corte
Segundo os cálculos da Sandvik Coromant, o custo das ferramentas pode representar 3 a 5% do custo de produção total. Ao ponderar-se a aquisição de uma ferramenta que se desgasta com o tempo, como, p. ex., uma pastilha de metal duro para o torneamento de aço, é natural ter-se unicamente em consideração o custo unitário inicial. Em vez disso, a Sandvik Coromant recomenda que os seus clientes lancem um olhar diferente às coisas e que reavaliem como levar em conta o custo das ferramentas na gestão de todo o processo de custos de produção, o que inclui despesas como a depreciação da maquinaria.
Se analisarmos um dia de trabalho típico numa oficina mecânica, digamos com dois turnos que totalizem 14,4 horas, 60% do tempo é dedicado à produção, ou tempo de corte, enquanto 40% do tempo é dedicado a outras coisas, ou seja, o tempo sem corte. Naturalmente, o objectivo aqui deve ser a redução do tempo sem corte e a maximização do tempo de maquinagem.
A melhor forma de o alcançar é manter o tempo de produção reduzido, aumentando, simultaneamente, a utilização da máquina-ferramenta. Na realidade, a Sandvik Coromant concluiu que um aumento de 20% na utilização da máquina pode assegurar um margem de lucro bruta 10% superior.
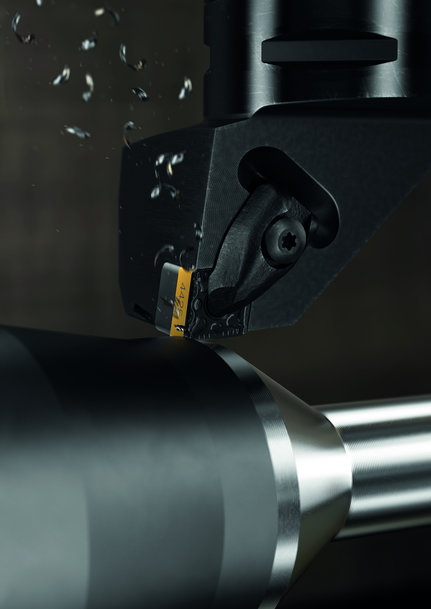
Vida útil prolongada da ferramenta
Os fabricantes medem as taxas de produção de várias formas, sendo uma delas o número de peças de trabalho concluídas ao longo de um determinado período de tempo. No entanto, diversos factores podem impedir os fabricantes de alcançarem o número pretendido de peças de trabalho por turno. A necessidade de substituições frequentes das pastilhas, as interrupções da produção e a incapacidade de encontrar a pastilha certa para cada aplicação ou material, são tudo questões consideradas como as principais responsáveis pelo desperdício de tempo na produção moderna.
De que forma podem os fabricantes superar estes desafios, trabalhando ao mesmo tempo com peças de trabalho duras em alumínio, aços não ligados e outros materiais? Nestes casos, a classe da pastilha deve ser seleccionada, primordialmente, pela sua adequação à peça de trabalho. Trata-se de um desafio, pois muitas variáveis podem afectar o desempenho da pastilha da ferramenta de corte, pelo que o fornecimento de uma única classe para satisfazer as vastas exigências das áreas P15 a P25 pode ser uma tarefa ingrata. P15 a P25 refere-se às exigências impostas por diferentes condições de trabalho aos parâmetros da máquina: dados de corte, acabamento de superfície, profundidade de corte, superfícies maquinadas ou irregulares, cortes contínuos ou interrompidos, são todos afectados.
Na realidade, há muitos pré-requisitos para qualquer classe que faça estas reivindicações. Por exemplo, a resistência à fractura é fundamental, assim como uma aresta de corte capaz de assegurar a dureza necessária para resistir a qualquer deformação plástica provocada pelas temperaturas extremas presentes na zona de corte. Além disso, o revestimento da pastilha tem de ser capaz de evitar o desgaste de flanco, o desgaste de cratera e a formação de aresta. É também crucial a aderência do revestimento ao substrato. Se o revestimento não aderir, o substrato fica exposto, o que pode conduzir a uma rápida falha.
Para evitar estes resultados, podemos dizer que a limitação do desgaste contínuo e controlável, bem como a eliminação do desgaste descontínuo e frequentemente incontrolável, são as chaves para o sucesso. Por outras palavras, o objectivo é o desgaste previsível da ferramenta. Não que a total previsibilidade seja fácil de alcançar, evidentemente, e em particular considerando a actual tendência do mercado para a maquinagem com supervisão limitada ou sem supervisão.
Em todo o caso, o padrão de desgaste ideal para qualquer pastilha é o desgaste de flanco controlado, pois resulta numa vida útil previsível das arestas de corte. A classe ideal é aquela que limita o desenvolvimento de tipos indesejados de desgaste e que, em algumas operações, evita em absoluto o seu desenvolvimento.
Para maximizar o número de peças produzidas, é vital seleccionar a pastilha de metal duro certa — e é também por isto que a Sandvik Coromant irá lançar um par de novas classes de metal duro para torneamento em P ISO na sua gama, designadas GC4415 e GC4425, que se referem a P15 e P25 respectivamente. A GC4425 fornece melhor resistência ao desgaste, resistência térmica e robustez, enquanto a classe GC4415 está concebida para complementar a GC4425 nos casos em que é necessário optimizar o desempenho e aumentar a resistência térmica.
Ambas as classes são ideais para a utilização com aço de baixa liga e não ligado. Podem maquinar um maior número de peças dentro de uma configuração de produção em massa e em série, contribuindo para um aumento da vida útil da ferramenta, eliminando rupturas repentinas e reduzindo os trabalhos de rectificação e a transformação em sucata.
As classes GC4415 e GC4425 incluem, cada uma delas, a tecnologia Inveio® de segunda geração, a orientação unidireccional dos cristais na camada de revestimento de alumínio. O que torna a Inveio única pode ser visto analisando o material a nível microscópico: a superfície do material caracteriza-se por uma orientação unidireccional dos cristais. Todos os cristais no revestimento de alumínio estão alinhados na mesma direcção, criando uma forte barreira face à zona de corte. A orientação dos cristais foi melhorada substancialmente no revestimento Inveio de segunda geração.
A Inveio assegura à pastilha uma elevada resistência ao desgaste e uma vida útil prolongada da ferramenta. As ferramentas mais duradouras são, evidentemente, benéficas para a redução do custo por peça. Adicionalmente, e para além de outros parâmetros de selecção, os engenheiros devem analisar de que forma a geometria de uma pastilha afecta o controlo de aparas e o desempenho de maquinagem.
Melhor geometria
Geometria refere-se ao estilo da própria pastilha, concebido de acordo com os tipos de maquinagem: acabamento, média e desbaste. Todas têm as suas próprias implicações no que respeita à velocidade de corte — a sua própria área de trabalho, com base numa ruptura de aparas aceitável relativamente à taxa de avanço e à profundidade de corte.
Para ajudar os clientes a optarem pelas melhores pastilhas de torneamento e classes em função dos seus requisitos, a Sandvik Coromant tornou possível a realização desta escolha online através do CoroPlus® Tool Guide.
No torneamento, os três principais parâmetros de corte: velocidade, avanço e profundidade de corte, produzem um efeito significativo na vida útil da ferramenta e, consequentemente, no custo por peça, tendo em conta que um aumento de 20% nos dados de corte pode baixar em 10% o custo de um componente. Um modelo desenvolvido no início do século XX pelo engenheiro mecânico americano, Frederick Winslow Taylor, estabeleceu a relação entre velocidade de corte, desgaste da ferramenta e vida útil da ferramenta.
Taylor concluiu que a utilização da maior profundidade de corte possível reduz o número de passagens de corte necessárias, diminuindo assim o tempo de maquinagem. Mas, alertou também que o torneamento de aço optimizado depende da estabilidade do suporte no qual a ferramenta é montada, da fixação da peça de trabalho e da aplicação de líquido de refrigeração para a máquina-ferramenta, bem como da potência da máquina-ferramenta.
Abordagem holística
O modelo de Taylor mostra-nos que o torneamento de aço optimizado vai para além de classes e geometrias. Em vez disso, os fabricantes devem ter em consideração todo o conceito de ferramentas. Tudo desde a classe da pastilha, o design do suporte e o porta-ferramentas pode aumentar o rendimento, reduzir custos e assegurar níveis superiores de segurança dos processos.
Esta abordagem holística alternativa foi posta à prova por um cliente no segmento de engenharia geral, usando a pastilha de metal duro GC4425 da Sandvik Coromant na produção de um veio. A GC4425 foi concebida para melhorar a resistência ao desgaste, a resistência térmica e a robustez. Além disso, tem a capacidade de trabalhar com dados de corte superiores. A pastilha foi utilizada num aço 4140 pré-tratado termicamente (PHT), um aço de liga e cromo-molibdénio com uma dureza de 40 HRC (ou dureza Rockwell C). A classe é normalmente utilizada em tudo, desde engrenagens e bombas, até várias aplicações nas indústrias automóvel e da construção.
A peça de trabalho 4140 PHT foi sujeita a um desbaste externo multi-direccional. No âmbito do teste, o desempenho da GC4425 foi comparado com o de uma pastilha ISO da concorrência, utilizada para o mesmo processo. Crucialmente, conseguimos aumentar a velocidade de corte (vc) e multiplicar a taxa de avanço (fn) — vc=183 m/min (600 pés/min) e fn=0,33 mm/rpm (.013 pol/rpm) com a pastilha da concorrência, contra 244 m/min (800 pés/min) vc e 0,51 mm/rpm (.020 pol/rpm) fn com a GC4425.
No final, a pastilha da Sandvik Coromant permitiu um aumento de produtividade de 100%, com uma redução de 50% do tempo de ciclo. Globalmente, o cliente alcançou uma redução de custos de 30%.
Este resultado mostra que, ao considerarem todo o conceito das ferramentas, os fabricantes podem alcançar uma produção mais rentável e um custo por peça mais baixo. Esta abordagem holística às classes de pastilhas, à geometria e à economia de produção geral será essencial, caso os fabricantes pretendam manter a sua competitividade face ao permanente impacto da COVID-19.
www.sandvik.coromant.com