www.engenharia-brasil.com
18
'11
Written on Modified on
Produção de recipientes de vidro para uso farmacêutico
A SPAMI, uma empresa do Grupo Stevanato, desenvolveu um sistema de inspecção para aumentar a qualidade do material de vidro. O sistema utiliza tecnologias de controlo de qualidade para examinar os tubos de vidro quando chegam à fábrica, bem como o produto final. O sistema é composto por um sistema de inspecção visual (NoVIS), um sistema para a medição contínua da temperatura e também um sistema de processamento da imagem digital, o chamado "CLEANER", que consegue detectar e remover falhas com o tamanho de alguns mícrones no vidro do produto final. As máquinas de processamento totalmente integradas realizam a medição do diâmetro do tubo de vidro, da espessura da parede e da temperatura utilizando pirómetros de infravermelhos (pirómetro para controlar o recozimento), para um controlo de qualidade total, e queimadores motorizados que garantem um controlo preciso do seu posicionamento. A utilização deste sistema concede à Stevanato a sua vantagem em termos de qualidade em relação aos outros fabricantes de frascos. Neste sistema avançado, a S.P.A.M.I. utiliza conversores Anybus da HMS para estabelecer a ligação entre as câmaras de inspecção visual remotas e o CLP que controla as linhas de produção.
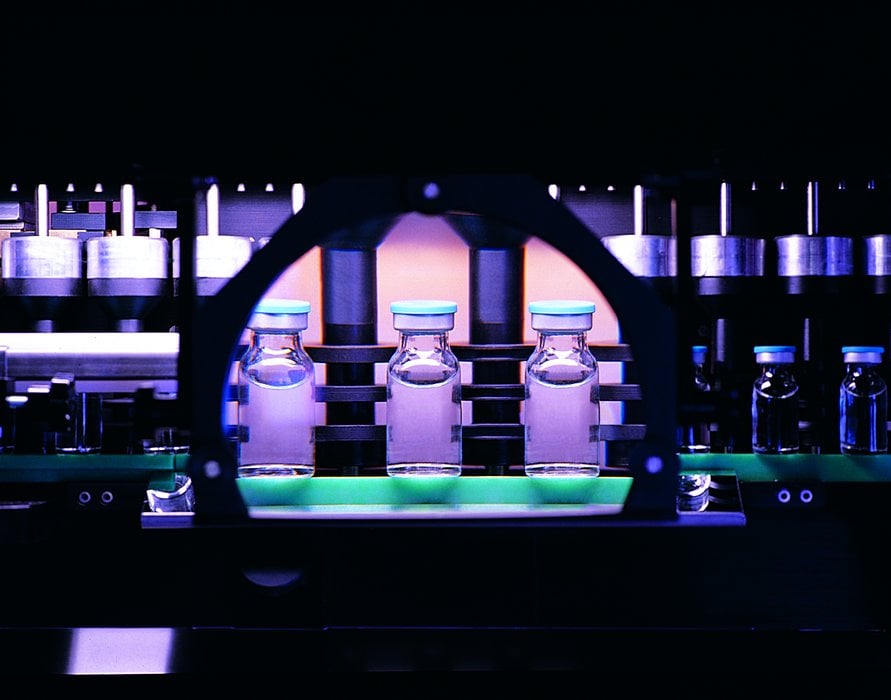
Fundada em 1949 como uma oficina de artesãos numa região com uma forte tradição no fabrico de vidro, o Grupo Stevanato é actualmente uma empresa industrial bem sucedida que produz sistemas de elevada tecnologia.
O Grupo é composto por dois departamentos. O Departamento de Vidro que está especializado na produção de embalagens primárias em tubos de vidro para o uso farmacêutico, disponibiliza uma vasta gama de produtos desde embalagens primárias tradicionais, tais como, ampolas e frascos, passando pelos produtos de crescimento rápido, tais como, cartuchos para auto-injectores e sistemas de injecção através de canetas, até às seringas esterilizadas e prontas a encher.
O Departamento de Engenharia composto pelas empresas S.P.A.M.I. e Optrel especializadas no design e na produção de máquinas e equipamentos para a conversão, inspecção visual e monitorização de recipientes feitos a partir de tubos de vidro. A sinergia entre as duas divisões assegura que o Grupo Stevanato mantenha o controlo total sobre todo o processo de produção, desde a compra de matérias primas até à assistência pós-venda.
"A produção da S.P.A.M.I. destina-se tanto para as empresas do Grupo como também para a venda a outras empresas externas." As soluções mecânicas e eléctricas instaladas nas máquinas formadoras foram concebidas para fornecer a maior precisão possível e os melhores resultados na produção de recipientes de vidro.
Todos os componentes utilizados para formar o vidro derretido são instalados e cuidadosamente verificados para garantir a tolerância dimensional dos frascos, das seringas, dos cartuchos e das ampolas. Os componentes instalados nas máquinas formadoras e nas cintas transportadoras foram especificamente seleccionados para evitar a contaminação dos recipientes. O processo é totalmente automático, desde a alimentação dos tubos até ao embalamento.
O ciclo de produção é iniciado com os tubos de vidro que são adquiridos externamente em peças de aprox. 1,5 m de comprimento e com um diâmetro adequado para o tamanho do produto final. Os tubos de vidro são colocados em máquinas formadoras rotativas com várias cabeças de processamento e são, em seguida, aquecidos por queimadores. Dependendo do ciclo do processo, que é seleccionado de acordo com o produto a ser produzido, a boca e o fundo do frasco, da ampola, da seringa, etc. são formados deste modo.
Na linha de produção é instalado o seguinte equipamento:
A jusante da máquina formadora está instalada uma cinta transportadora onde são realizadas inspecções cosméticas e de âmbito dimensional através de câmaras de modo a assegurar uma verificação meticulosa dos recipientes de vidro. "Isto são basicamente medições em relação às dimensões que são realizadas através da análise das imagens", explica Gobita. "Visto que o produto está sujeito a esforço mecânico durante o processamento, existe também um forno de recozimento que fornece um ciclo térmico para eliminar a tensão criada no vidro." Depois, a fase final inclui o controlo de qualidade do produto final e o embalamento automático. É necessário alertar para o facto desta parte final do ciclo ser executada de modo a assegurar o nível de qualidade e a esterilização necessária para a utilização em aplicações farmacêuticas.
São várias as empresas da concorrência no mercado que operam a nível internacional. "Os nossos principais concorrentes são alemães e americanos, enquanto as outras empresas na Itália são consideravelmente mais pequenas que a nossa", referiu Gobita.
A mais-valia oferecida pela S.P.A.M.I. prende-se, principalmente, com o nível da qualidade dos seus produtos, o que permitiu ocupar um lugar de destaque neste sector." Desde que são usados nas aplicações farmacêuticas, os nossos produtos possuem padrões de qualidade muito elevados e estão sempre em conformidade com os limites reguladores muito exigentes. Isto requer um grande número de controladores de qualidade altamente qualificados", continuou Gobita. "A diferença entre nós e os nossos concorrentes nacionais prende-se com esse mesmo aspecto. A nossa capacidade de pesquisa e desenvolvimento também é um factor: quando as empresas farmacêuticas pedem amostras que sejam diferentes dos produtos padrão, conseguimos apresentar um produto com design diferente porque podemos alterar o nosso sistema. Tal como o departamento mecânico que produz os sistemas dentro do Grupo, a S.P.A.M.I. consegue alterar e adaptar esses sistemas de modo a satisfazer os requisitos de produção. Esta capacidade de personalizar os sistemas é outra mais-valia importante que podemos oferecer aos nossos clientes. É necessário lembrar que existem vários produtos normalizados no sector farmacêutico, tais como ampolas e frascos que todos nós conhecemos, mas também existem muitos produtos especiais, cujos números continuam a aumentar, que, na maioria das vezes, são desenvolvidos ad hoc. Para isso, é necessário uma máquina específica e a máquina pré-existente tem de ser alterada na maioria das vezes".
Uma colaboração positiva com a HMS
A cooperação com a HMS resultou da vontade de querer resolver um problema de comunicação específico.
Uma aplicação estava a ser desenvolvida pelo departamento mecânico no sentido de realizar um conjunto de controlos de qualidade do produto com base na tecnologia óptica da máquina. Mais concretamente, as câmaras inteligentes Cognex tinham que estabelecer a ligação com o CLP da Siemens. "Necessitávamos que as câmaras com interface Ethernet comunicassem com o CLP através do protocolo Profibus", explicou Gobita. "Após alguma pesquisa cuidadosa, e através da EFA Automation, o distribuidor exclusivo na Itália das soluções GATEWAY da HMS, conseguimos encontrar um dispositivo Anybus que permite resolver o problema de comunicação entre o nosso equipamento."
Outros potenciais fornecedores foram levados em consideração nessa altura, mas a HMS foi a única empresa que conseguiu disponibilizar uma vasta gama de conversores de protocolo. "Esta vasta disponibilidade foi fulcral para a nossa escolha, pois as nossas diversificadas aplicações são muitas vezes diferentes umas das outras. No início, por exemplo, necessitávamos de gerir o protocolo Profibus visto que era utilizado pelo CLP da Siemens, mas, normalmente, a nossa empresa também utiliza controladores programáveis de outros fornecedores. Assim, é essencial para nós possuir uma vasta gama de produtos." O primeiro produto HMS utilizado foi um dispositivo da gama de conversores Anybus que converte o protocolo Profibus para o Modbus via Ethernet: o Anybus X-gateway.
Existe a possibilidade de instalar mais do que um conversor Anybus em cada linha de produção. "Até agora, usámos vários conversores devido ao facto da aplicação ter sido usada em vários sistemas", continua Gobita. "As câmaras inteligentes são usadas para verificar os vários aspectos de qualidade do produto e têm de ser instaladas em diferentes locais do sistema. Basicamente, isto não é uma aplicação »única« dos conversores HMS, mas uma aplicação que se tornou um padrão para nós." "Estamos muito satisfeitos com a nossa escolha. Os produtos Anybus da HMS são muito completos, funcionais e fáceis de usar em comparação com outros dispositivos similares que experimentámos. Todos sabemos que é muito fácil encontrar coisas complexas, mas não é tão fácil encontrar coisas simples.
Não tivemos qualquer tipo de problema, nem na maneira como as coisas se desenvolveram. No futuro estamos a planear usar os conversores Anybus da HMS em outras linhas para que estas estejam ligadas aos nossos sistemas de controlo através de câmaras. E, visto que os padrões requerem tolerâncias cada vez mais reduzidas, é inevitável que haja cada vez mais verificações através de câmaras remotas", concluiu Gobita.
O Grupo é composto por dois departamentos. O Departamento de Vidro que está especializado na produção de embalagens primárias em tubos de vidro para o uso farmacêutico, disponibiliza uma vasta gama de produtos desde embalagens primárias tradicionais, tais como, ampolas e frascos, passando pelos produtos de crescimento rápido, tais como, cartuchos para auto-injectores e sistemas de injecção através de canetas, até às seringas esterilizadas e prontas a encher.
O Departamento de Engenharia composto pelas empresas S.P.A.M.I. e Optrel especializadas no design e na produção de máquinas e equipamentos para a conversão, inspecção visual e monitorização de recipientes feitos a partir de tubos de vidro. A sinergia entre as duas divisões assegura que o Grupo Stevanato mantenha o controlo total sobre todo o processo de produção, desde a compra de matérias primas até à assistência pós-venda.
"A produção da S.P.A.M.I. destina-se tanto para as empresas do Grupo como também para a venda a outras empresas externas." As soluções mecânicas e eléctricas instaladas nas máquinas formadoras foram concebidas para fornecer a maior precisão possível e os melhores resultados na produção de recipientes de vidro.
Todos os componentes utilizados para formar o vidro derretido são instalados e cuidadosamente verificados para garantir a tolerância dimensional dos frascos, das seringas, dos cartuchos e das ampolas. Os componentes instalados nas máquinas formadoras e nas cintas transportadoras foram especificamente seleccionados para evitar a contaminação dos recipientes. O processo é totalmente automático, desde a alimentação dos tubos até ao embalamento.
O ciclo de produção é iniciado com os tubos de vidro que são adquiridos externamente em peças de aprox. 1,5 m de comprimento e com um diâmetro adequado para o tamanho do produto final. Os tubos de vidro são colocados em máquinas formadoras rotativas com várias cabeças de processamento e são, em seguida, aquecidos por queimadores. Dependendo do ciclo do processo, que é seleccionado de acordo com o produto a ser produzido, a boca e o fundo do frasco, da ampola, da seringa, etc. são formados deste modo.
Na linha de produção é instalado o seguinte equipamento:
A jusante da máquina formadora está instalada uma cinta transportadora onde são realizadas inspecções cosméticas e de âmbito dimensional através de câmaras de modo a assegurar uma verificação meticulosa dos recipientes de vidro. "Isto são basicamente medições em relação às dimensões que são realizadas através da análise das imagens", explica Gobita. "Visto que o produto está sujeito a esforço mecânico durante o processamento, existe também um forno de recozimento que fornece um ciclo térmico para eliminar a tensão criada no vidro." Depois, a fase final inclui o controlo de qualidade do produto final e o embalamento automático. É necessário alertar para o facto desta parte final do ciclo ser executada de modo a assegurar o nível de qualidade e a esterilização necessária para a utilização em aplicações farmacêuticas.
São várias as empresas da concorrência no mercado que operam a nível internacional. "Os nossos principais concorrentes são alemães e americanos, enquanto as outras empresas na Itália são consideravelmente mais pequenas que a nossa", referiu Gobita.
A mais-valia oferecida pela S.P.A.M.I. prende-se, principalmente, com o nível da qualidade dos seus produtos, o que permitiu ocupar um lugar de destaque neste sector." Desde que são usados nas aplicações farmacêuticas, os nossos produtos possuem padrões de qualidade muito elevados e estão sempre em conformidade com os limites reguladores muito exigentes. Isto requer um grande número de controladores de qualidade altamente qualificados", continuou Gobita. "A diferença entre nós e os nossos concorrentes nacionais prende-se com esse mesmo aspecto. A nossa capacidade de pesquisa e desenvolvimento também é um factor: quando as empresas farmacêuticas pedem amostras que sejam diferentes dos produtos padrão, conseguimos apresentar um produto com design diferente porque podemos alterar o nosso sistema. Tal como o departamento mecânico que produz os sistemas dentro do Grupo, a S.P.A.M.I. consegue alterar e adaptar esses sistemas de modo a satisfazer os requisitos de produção. Esta capacidade de personalizar os sistemas é outra mais-valia importante que podemos oferecer aos nossos clientes. É necessário lembrar que existem vários produtos normalizados no sector farmacêutico, tais como ampolas e frascos que todos nós conhecemos, mas também existem muitos produtos especiais, cujos números continuam a aumentar, que, na maioria das vezes, são desenvolvidos ad hoc. Para isso, é necessário uma máquina específica e a máquina pré-existente tem de ser alterada na maioria das vezes".
Uma colaboração positiva com a HMS
A cooperação com a HMS resultou da vontade de querer resolver um problema de comunicação específico.
Uma aplicação estava a ser desenvolvida pelo departamento mecânico no sentido de realizar um conjunto de controlos de qualidade do produto com base na tecnologia óptica da máquina. Mais concretamente, as câmaras inteligentes Cognex tinham que estabelecer a ligação com o CLP da Siemens. "Necessitávamos que as câmaras com interface Ethernet comunicassem com o CLP através do protocolo Profibus", explicou Gobita. "Após alguma pesquisa cuidadosa, e através da EFA Automation, o distribuidor exclusivo na Itália das soluções GATEWAY da HMS, conseguimos encontrar um dispositivo Anybus que permite resolver o problema de comunicação entre o nosso equipamento."
Outros potenciais fornecedores foram levados em consideração nessa altura, mas a HMS foi a única empresa que conseguiu disponibilizar uma vasta gama de conversores de protocolo. "Esta vasta disponibilidade foi fulcral para a nossa escolha, pois as nossas diversificadas aplicações são muitas vezes diferentes umas das outras. No início, por exemplo, necessitávamos de gerir o protocolo Profibus visto que era utilizado pelo CLP da Siemens, mas, normalmente, a nossa empresa também utiliza controladores programáveis de outros fornecedores. Assim, é essencial para nós possuir uma vasta gama de produtos." O primeiro produto HMS utilizado foi um dispositivo da gama de conversores Anybus que converte o protocolo Profibus para o Modbus via Ethernet: o Anybus X-gateway.
Existe a possibilidade de instalar mais do que um conversor Anybus em cada linha de produção. "Até agora, usámos vários conversores devido ao facto da aplicação ter sido usada em vários sistemas", continua Gobita. "As câmaras inteligentes são usadas para verificar os vários aspectos de qualidade do produto e têm de ser instaladas em diferentes locais do sistema. Basicamente, isto não é uma aplicação »única« dos conversores HMS, mas uma aplicação que se tornou um padrão para nós." "Estamos muito satisfeitos com a nossa escolha. Os produtos Anybus da HMS são muito completos, funcionais e fáceis de usar em comparação com outros dispositivos similares que experimentámos. Todos sabemos que é muito fácil encontrar coisas complexas, mas não é tão fácil encontrar coisas simples.
Não tivemos qualquer tipo de problema, nem na maneira como as coisas se desenvolveram. No futuro estamos a planear usar os conversores Anybus da HMS em outras linhas para que estas estejam ligadas aos nossos sistemas de controlo através de câmaras. E, visto que os padrões requerem tolerâncias cada vez mais reduzidas, é inevitável que haja cada vez mais verificações através de câmaras remotas", concluiu Gobita.